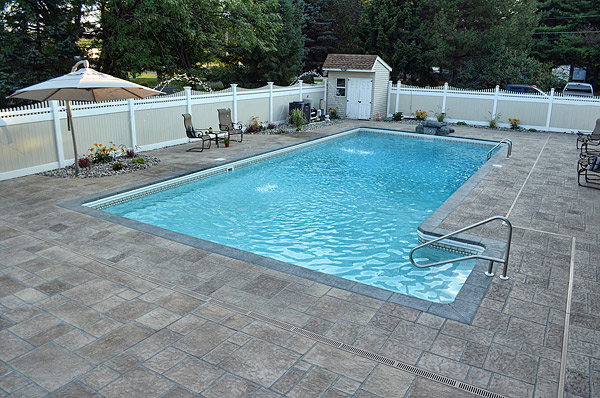
When taking the plunge into a pool construction or renovation project, don’t forget the stormwater drainage.
That’s the pool drain 101 lesson from Todd Fisher of Unique Concrete in West Milford, New Jersey, who has seen a big upturn in the pool restoration/upgrade segment of the company’s decorative concrete business. Pool decks and coping account for the lion’s share of jobs in that market, he says.
“There are a lot of old pools in the area here,” Fisher says, speaking of the company’s market base in northern New Jersey. Besides the abundance of aging pools, the segment’s growth is driven by upscale demographics in major portions of the area’s diverse residential mix.
In commercial and many high-end residential pool projects, a designer is typically involved in the pool construction or improvement project, and in those cases contractors such as Unique Concrete follow the architect or other designer’s plans and specifications. “In those cases we don’t have much leeway” in the details on drains, Fisher says.
But in typical residential pool projects, the contractor needs to gauge existing or potential stormwater drainage issues to ensure that water flows away from pavements and structures. In Unique Concrete’s neck of the woods, the area’s hilly terrain also can present stormwater drainage complications, especially if the pool is in a low spot amid higher surroundings.
“The problems are often due to a structure — a house or a pool house or other building — that limits where we can get rid of the water,” Fisher explains.
Fisher cites a major pool upgrade in 2014 at a residence in Augusta, New Jersey, as an illustration of the drain connection in pool construction and restoration.
Gauging the problem
Unique Concrete doesn’t do cartwheels when the prospect of installing drains emerges in a project, Fisher says. “If you can find creative ways to handle runoff without drains, that’s preferable,” he says. Besides the cost of installing the drains, the owner must deal with ongoing maintenance issues associated with debris and clogs.
In the case of the Augusta project, Unique Concrete and the homeowner knew there was a drainage problem. The job of installing a drain system was going to be challenging because the plan involved resurfacing the existing concrete deck, adding a new section and replacing pavers with concrete.
In the renovation, a lengthy drain course was required to transport the water to the adjacent landscape. When originally installed, the pool, deck and adjacent patio pavers had been installed without a drain system. This caused problems due to water running away from the pool but toward the pavers and home foundation. Fisher says he devised a “creative solution” by locating a channel drain between the existing concrete and the new slab that replaced the pavers. Both sections slope toward the new channel drain.
A stamp pattern — Random Ashlar stone — was employed on concrete-overlay surfaces installed on top of the newly placed concrete and the existing concrete.
Crucial connection
The drain was installed prior to pouring the new section of deck, with the drain channel running the length of the deck. The drain trench was prepared, and the channel drain was temporarily put in place as a mockup. Concrete footings were poured at intervals of 5 to 7 feet. The channel drain was then put in place on the footings, prior to pouring new concrete.
Fisher says a key task in the deck/drain installation is placing reinforcement rods in the newly poured concrete surfaces and connecting them to the channel drain. The reinforcement runs horizontally from one concrete slab to the other and connects to the drain between the slabs. Stegmeier LLC, the supplier of the major portion of the project’s drain system, notes the importance of this connection in its installation guide, Fisher says.
This channel drain’s connection to both concrete surfaces ensures that any natural movement of the concrete slabs affects the concrete and drain structure in tandem — as a unit — to prevent damage to the individual elements of the assembled structure.
For drain-system components, Unique Concrete went with Deck Drain for most of the drain course, but switched to a larger channel drain from NDS Inc. — the Spee-D, made of polyolefin — for a more expansive deck area where heavier volumes of water would occur.
Fisher says Unique Concrete has found the Deck Drain to be “user friendly” and, due to low profile and color choices, can be made to essentially “disappear” or blend into the decorative pavement surface.
“Since our work is decorative concrete, customers are spending money on something that looks good,” Fisher says. The Stegmeier drains “look good,” are functional and are offered in various colors that blend with decorative concrete surfaces.
The owner and contractor certainly don’t want a functional element — a stormwater-control system — to mar a decorative-concrete masterpiece.
“If we can find creative ways to handle runoff without drains, that’s preferable,” Fisher says. “But water sitting on a concrete slab can be a major problem and a legal problem. You’ve got to get rid of the water.”