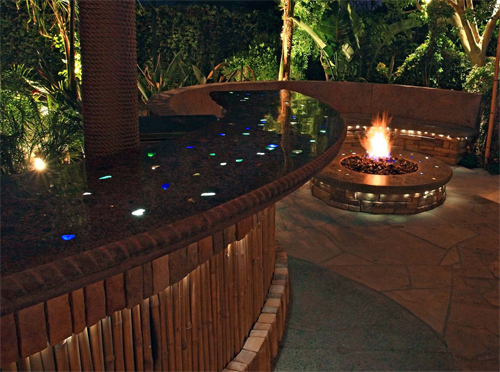
Mood lighting. Special effects. Animated logos. All of these and more can be integrated with decorative concrete, thanks to fiber optics.
Everyone has seen novelty fiber optic decorations – bunches of clear fibers emitting points of colored light from their ends. Designers use these same fibers to carry light to the surfaces of unique, high-end concrete counters, bars, pools and floors.
![]() |
![]() |
The fibers are composed of an acrylic core with a very thin cladding of denser acrylic, according to Cyr Ryan, owner and president of Fiber Optic Systems Inc., a fiber-optic installation creator in Whitehouse Station, N.J. The cladding acts as a mirror, reflecting light that enters one end of the fiber back and forth along the length of the fiber until it exits the other end.
The beauty of optical fibers for concrete is that there are no fixtures to embed, no individual light bulbs to burn out and no heat transferred to the surface. The light comes from an illuminator box installed in a cabinet, under the counter, in a subfloor or any nearby place where there is easy access to the bulb that lights the ends of the fibers. The box also houses a wheel that changes the color or brightness of the light.
The diameter of the optical fiber will determine how much light is emitted, but there are other factors to consider in choosing a fiber. Dominick Cardone, owner of The Concrete Impressionist Inc., Brooklyn, N.Y., says the fiber must be thick enough to resist breaking, flexible enough to bend and small enough to be invisible when the light is turned off. Ryan recommends a fiber of 1.5 mm diameter to meet these requirements and still get enough light to make an impact.
Once the fibers are embedded in the concrete, they will conduct light and last as long as the concrete itself. “I’ve had fiber optic pieces in place 15 years now and haven’t had an issue,” says Jeff Kudrick, product manager for J&M Lifestyles LLC, Randolph, N.J.
Two casting techniques
A decorative concrete installation with fiber optics begins with the right mix. “Mix designs need to be very fluid or respond well to vibration so the concrete will flow and encapsulate the fibers,” explains Jeffrey Girard, P.E., president of The Concrete Countertop Institute. Many contractors specializing in fiber optics formulate their own mixes, though a countertop bag mix may be used as long as it can be made fluid enough.
Countertops with fiber optics may be precast or cast in place. The most common technique is precast. Dominick Cardone’s method is a good example of how to install fiber optics in precast countertops, though every contractor will have his or her own personal style.
Following a stencil prepared by his lighting supplier, Cardone drills tiny holes, one for each fiber, in a birch plywood mold laminated with mica. (He warns that a melamine mold will expand if water gets into those holes.) There may be several hundred or even thousands of holes required.
Once the holes are drilled and the rebar placed, Cardone inserts a fiber through each hole by hand, extending about 1/4 inch to 3/8 inch past the mold. He gives the fiber a light tug at an angle perpendicular to the drilled hole to make sure it is secure. He places fiber bundles and labels them according to the illumination plan, then runs the bundles along the rebar, attaching them with zip ties, until they reach the point where they will exit the slab and connect to the illuminator box.
When he pours the concrete, he uses his fingers to flow it around the fibers. He vibrates it well to be sure it is consolidated so the fibers can’t come loose. Two or three days after the pour, he inverts the mold on the edge of a table so the fiber bundles coming out of the concrete can hang freely.
![]() |
![]() |
Then comes the challenge of removing the mold. “Remember, you’ve got fibers sticking out of the top,” he cautions. “You can’t just slide the mold off – you’ll break off the fibers.” So he inserts cedar shims between the concrete and form all the way around. When the mold is loose he lifts it straight up. The fiber ends protrude above the concrete like whiskers. Using a widget with a single-edge razor blade he cuts the fiber tops off, making them even with the concrete surface.
At this point the counter can be ground and polished like any other precast concrete creation.
Once the counter is installed, the fiber bundles are connected to the illuminator through a metal plate that attaches to the box housing the light and the color wheel. Cardone pushes the bundles one by one through the holes in the plate according to the program pattern. He uses a hot wire to cut the ends of the fibers, which gives a clean end for maximum light transmission and expands the fibers slightly so they won’t pull out of the plate.
This method of precasting with optical fibers creates a look with pinpoints of light that can change color, twinkle, or appear to chase each other. Scott Cohen, author of “Scott Cohen’s Outdoor Kitchen Design Workbook” and garden artisan for The Green Scene Inc., based in the San Fernando Valley, Calif., creates a very different look in his outdoor kitchens with cast-in-place counters. He doesn’t run the fiber all the way to the concrete surface for a single bright point. Instead, he diffuses the points of light by attaching fibers to chunks of colored glass with a hot glue gun. He uses one or two fibers for smaller or light-colored glass, two or three fibers for darker colored glass.
With the fibers attached, Cohen sets the glass in dollops of high-performance concrete at the anticipated top of the piece. After pouring concrete around the dollops, he vibrates it to consolidate it. To avoid damaging the fibers, he runs the vibrator outside and underneath the form. When the concrete is cured he grinds and polishes it, finishing with a penetrating sealer or protective coating as the application requires.
A unique offering for customers
Concrete with fiber optics is not for everyone. Not every contractor can tolerate the repetitive task of inserting hundreds of tiny fibers or keeping track of where each one goes. Not many businesses or homeowners can afford the added cost. (Cohen adds $3,200 to a countertop job to cover the illuminator plus 300 fibers and large pieces of glass, and that is on top of an additional upgrade from plain cast concrete to polished hand seeded glass). But for those what want a truly unique look or are looking for a stunning effect, fiber optics are a cool, versatile option.
Cyr Ryan thinks the use of fiber optics in decorative concrete is poised to expand beyond countertops and bars. “There’s no reason why you can’t use light animation in floors and walls,” he says. “It’s just using your imagination.”
Fiber optic lighting specialists
These are some of the country’s leading experts in working with fiber optic lighting installations in concrete.
The Concrete Impressionist Inc.
www.concreteimpressionist.com
Fiber Optic Systems Inc.
www.fosi.com
The Green Scene
www.greenscenelandscape.com
J&M Lifestyles LLC
www.jmlifestyles.com