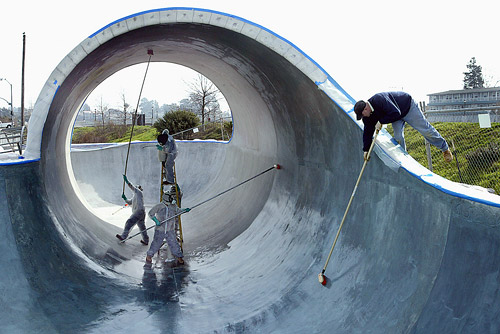
Skate Park at Mike Fox Park, Santa Cruz, Calif. Restoring and laying an overlay onto the concrete floor at this 80,000-square-foot outdoor mall project presented just about every challenge a concrete contractor could imagine.
At first, skateboarding and decorative acid-stained concrete may not seem to have much in common, but think freedom, creativity, passion — sheer love of the art — and you’ll see the two were meant for each other.
In 1974, Wormhoudt Inc. built the world’s first public skate park in Santa Cruz, Calif. So it was fitting that more than two decades later, the city of Santa Cruz went back to the experienced firm for a new skate park inside Mike Fox Park. Architect and skater Zach Wormhoudt was not put off by the 10 years it took to bring this park to life. “There is a lot of community participation in a project like this, including a lot of outreach to skaters,” he says.
Zach Wormhoudt, who has designed a hundred skate parks all over the world, took over this project after the death of its the original architect, his father Ken Wormhoudt.
Long before construction began, Wormhoudt had been thinking about how to color the park. He had worked with Tom Ralston, owner of Tom Ralston Concrete in Santa Cruz, to have accents in an earlier park acid-stained, and together they thought it was time to bring this technique to an entire project.
![]() |
![]() |
![]() |
But first there had to be concrete to stain. A.J. Vasconi General Engineering, of Concord, Calif., won the bid to build the park as well as engineer and pour the concrete. Wormhoudt had worked with Andy Vasconi, president and founder, on Vasconi’s first skate park in 1999, and this partnership was vital to the success of the Santa Cruz project.
Vasconi was a civil engineer who began his career working with a bridge-building contractor. After he started his own small firm, while building up the capital required to get back into building bridges, he took on smaller concrete projects and soon gravitated to skate parks where he could use his engineering background. In fact, Vasconi has completed 20 skate parks in the past eight years, and the parks account for about one-third of his business every year.
The Santa Cruz project involved some detailed engineering and concrete work. The first challenge was logistics. The park was bounded by a river and canal, so work had to be staged from one end to the other, not approached from all sides. The second was evaluating — and eventually strengthening — the retaining wall next to the canal.
Third was the water table, just a foot or two below grade. Vasconi installed a French drain system of slotted pipe and crushed gravel to relieve water pressure that could have heaved the concrete above. Then he built up walls to contain engineered fill material so he could build the park above the original grade.
Then the fun began. The team poured concrete for the pools, bowls, decks and curved transitions that are the signature features of skate parks. Empty swimming pools are favorites of skaters, so this design included a large pool with bull-nose coping on top of a tile surround to duplicate the swimming pool skate experience, right down to the sound created by skating over tile. Tile is fragile, so Wormhoudt specified stamped concrete instead. Vasconi’s team imprinted a design around the pool edge and artist Dave Gardner hand-colored each “tile” with stain to create the look of a swimming pool.
The biggest challenge was the 16-foot-tall full pipe. “The structure of this full pipe is unique — its form, the way it mimics an ocean wave,” Wormhoudt says. “I don’t know of another structure like it.” Normally a full pipe is cut off at an angle perpendicular to its length. In this one, the top peaks at 23 feet wide and falls, wavelike, to just 12 feet wide where it meets the deck. The pipe wraps up and over in the same way that a wave breaks, giving skaters transitions where they can perform lots of tricks. “But,” says Wormhoudt, “it is really difficult to build. It is hard to get concrete to go into these shapes.”
Here Vasconi’s engineering expertise really paid off. He used bridge technology, steel beams and heavy timbers to build curved joists. He covered this truss system with sheet metal and placed the concrete on top of that.
Vasconi used shotcrete that consisted of a 3/8-inch aggregate and high cement content (7.5 sacks), delivering 4,000 psi of strength. It also contained fiber mesh to prevent shrink cracking during hydration. The shotcrete was pumped with a 2-inch concrete pump and shot onto the form through an air-powered nozzle. The finish was burned in with small fresnos or “funny trowels.”
The finish is important. Vasconi says, “We’re not building the court to play on, we’re building the ball to play with. It has to be perfectly round. We burn in the concrete so it is what the skaters call ‘buttery’ — fast and smooth.”
After the concrete was placed, it was turned over to Tom Ralston for staining. Vasconi’s crews helped power-wash the concrete, and then Ralston got to work. The city’s Department of Parks and Recreation wanted warm colors that evoked the ocean, and signed off on a blue-green called “Copper Patina” from L.M. Scofield Co. for the pools and bowls and a rich sand color, “Malay Tan” from Kemiko, for the decks. Acid stains were selected over other coloring options because of their vivid, permanent, penetrating colors.
For someone as experienced as Tom Ralston, much of the staining for the 15,000-square-foot park was routine. Staining the interior of the full pipe was another matter. Ralston says he sat and thought through how to go about staining overhead. He considered, and discarded, the idea of scaffolding and settled instead on sprayers with nozzles so the stain could be directed at an angle away from the workers below. These workers would be covered from head to toe in protective clothing. Crews of four, sometimes as many as eight, worked every day for two weeks to prep, stain, wash and neutralize, removing the water and ammonia with a vacuum and hauling it away.
The system worked — no worker was exposed to the stain. Ralston and Wormhoudt decided not to seal the concrete because they did not want a shiny, slippery surface. Not sealing also simplifies graffiti repair. When graffiti had to be removed shortly after the park’s opening, they simply power-washed it immediately and reapplied stain to the affected area.
![]() |
![]() |
There was still one more step to finish off the skate park. The outside of the wave was the perfect spot for a piece of public art, and that idea was built into the plans from the inception. Graphic designer (and renowned skater) Judi Oyama won the bid with a drawing by local artist Jimbo Phillips reminiscent of the ubiquitous doodles made by Santa Cruz surfers. The other member of the winning team was decorative concrete contractor Dave Pettigrew of Diamond D Concrete, based in Capitola, Calif. Once the proposal was accepted, Pettigrew faced the daunting task of turning a drawing on an 8 1/2-by-11 sheet into a 23-foot sandblasted stencil.
Pettigrew took the drawing to a sign maker who printed out a full-size stencil on two-foot sheets of paper. Meanwhile, he power-washed the wave and applied a custom-blended, sea-mist-colored acid stain. After letting it cure for a day, he applied another coat of stain and washed it. The next day he applied a blast mask — 1/8-inch rubber with an adhesive back. He attached the paper stencil to the mask, cut out the relief areas and removed the stencil, peeling off the cut areas of the mask as well.
The next step was to sandblast the exposed areas to the depth below the stain. Finally, the mask was removed and a shiny antigraffiti coating was applied to the remaining blue areas. The sandblasted concrete was left uncoated to create a textural contrast. Now it truly looks like a crashing wave, permanently preserved in concrete.
The skate park opened February 2007. There are various measures of its success. “Skaters’ demand for excellence in design is extremely high,” Vasconi says. “They are very honest on their Web sites about your work. When hardcore skaters leave you phone messages at 2 a.m. saying ‘You’re the best — keep it up,’ that’s when it’s worth it.”
Wormhoudt reports that the park’s reputation is spreading, and skaters from as far away as Europe are turning up to try it out. “The place is just packed every day,” Pettigrew adds. “It’s wonderful to work on a piece of art that is so functional.”