For contractors who want a rock finish on the exterior of an ICF structure, Marc Winkelman and Jim Jenkins, co-founders of CMJ Systems in McMinnville, Oregon, offer a variety of panelized stone veneer systems and interlocking structural insulated home-building panel systems.
”Our panels are revolutionizing the way homes are built and how stone veneer is applied,” says Winkelman.
CMJ is casting sheets of veneer stone in various sizes and seven different styles. To join them to the bucks or tie-ins built into the foam exterior, the sheets are simply attached with screws.
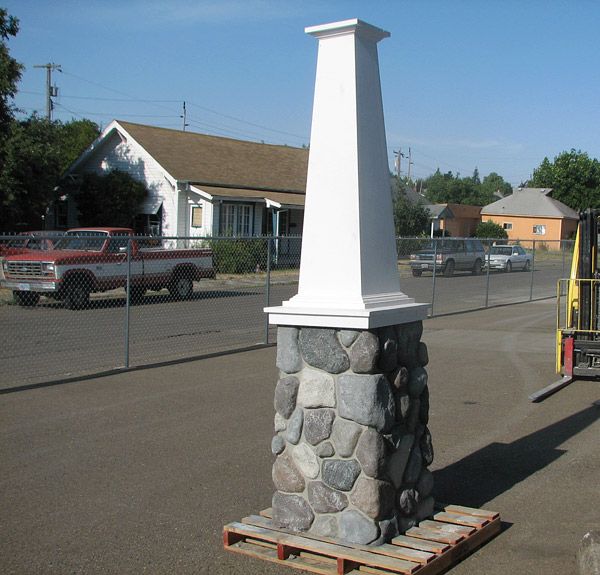
“Typically, a customer will give us the dimensions of the building either by blueprint or by actually measuring the physical structure,” Jenkins explains. “Once they give us the dimensions, we custom-cast panel assemblies that interlock and are precisely the sizes needed.”
Panel sizes range from 1-by-4 feet up to 12-by-12 feet, but because building sizes are often fluid, Jenkins says it’s also possible to cast exacting custom dimensions in the molding process developed by CMJ Systems.
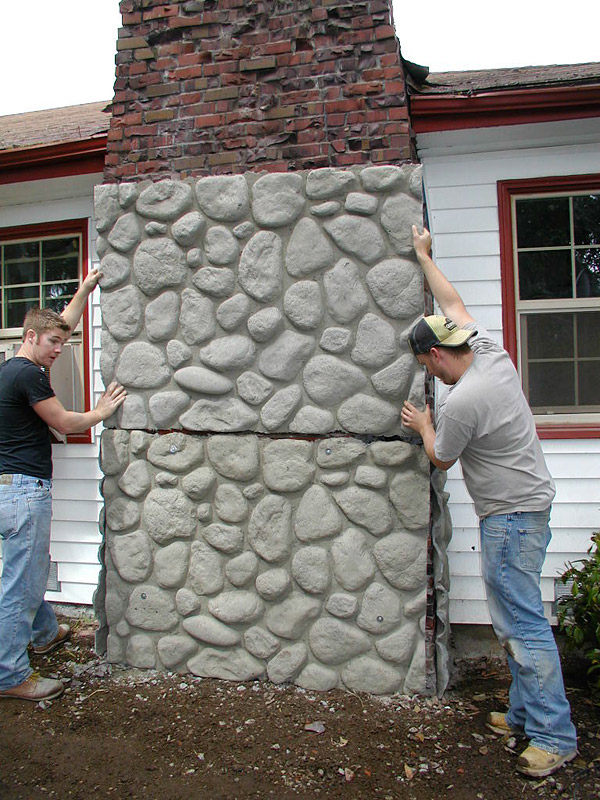
Panels are delivered in sequential order so they can be quickly and easily installed. From the time an order is placed until it shows up at the jobsite on the back of a semi-truck is approximately 30 days.
The look of the finished product varies by client.
“The most popular style is the stacked stone, with a dry-stacked look,” Jenkins says. “That’s followed in order by limestone panels, river rock, brick and then fieldstone.”
Panels are manufactured with pre-formed conduit through insulation for electrical and plumbing both vertically and horizontally.
Although the stone styles are limited, “We don’t have any color charts; we custom color every project,” he says.
“The best thing about our design is only 5 percent of the panel actually touches the structure,” Jenkins concludes. “In other words, there’s an air space that allows for condensation and air flow.”
www.cmj.systems