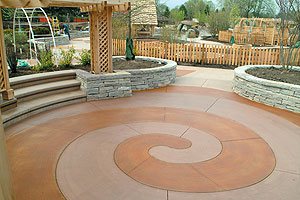
The boom in architectural concrete that started in the 1990s has created a great opportunity for both creativity and increased profitability for concrete contractors. But experienced installers know that success in this growing market depends on craftsmanship and attention to detail, even with a process that seems as straightforward as placing integrally colored concrete.
Why? Because customers and designers have different (higher!) expectations for the results of integrally colored concrete than they do for traditional gray. Art Tyson, color product specialist for Grace Construction Products, explains, “There is greater interest and more emotion behind color from the customer standpoint. Blemishes are more easily tolerated in gray concrete. Most issues that arise are basic concrete issues, not color issues, but the interest in color heightens them more.”
Great expectations
A quality job that results in a satisfied customer starts and ends with managing expectations. While we sometimes think of concrete as the ultimate man-made substance, it is more realistic to remind customers that it is in fact composed of natural materials and finished by hand. Minor variations are part of its charm and make each project unique. At the same time, a charming variation is quite a different thing from a contractor error, a difference that will be explored in depth later in this article.
The customer should not be the only one with great expectations. The most successful projects are those where everyone — ready-mix producer, contractor, designer and customer — all agree in advance on the standards and goals for the project and then remain consistent through the whole process.
Customers will have a better idea of what to expect if they see other completed jobs. The ideal situation is to make a mock-up using all the same materials and finishes that will be used on the job and then to ensure that no one deviates from that standard.
The mix
Consistency begins with the ready-mix producer. Steve Somerville, product line manager with Degussa Admixtures Inc., says, “We advise concrete producers to keep the mix consistent in order to keep the color consistent. It is important to maintain the same water-to-cement ratio and use the same aggregates and cementitious materials in every batch for the project. Once all parties agree on the mix design and the mock-up, consistency will guarantee customer satisfaction.”
An important part of the mix is the coloring agent. Integral color can either be added by the ready mix producer or mixed on site. In either case, careful measurement, quality control and consistency are critical. Liquid colors and quality powdered pigments contain dispersing agents that help deliver even color through the batch and consistency from batch to batch. Colors are also available in water-reducing admixtures that compensate for the higher water requirements of the coloring agent. Rich Solomon, president of Solomon Colors, points out, “It is up to the color manufacturer to supply a color shade that is uniform from lot to lot and batch to batch. From there it is up to the ready-mix producer to use the same products consistently.”
Most suppliers of coloring agents recommend four-inch slump. This is adequate for workability, but keeps color deep and bright while minimizing the risk of efflorescence caused by excess water evaporation. If for some reason greater slump is required, a water-reducing admixture is recommended instead of adding water. Careful review of technical instructions from color suppliers and even direct consultation as needed will prevent problems.
On the Job
Like traditional concrete, integrally colored concrete will perform best if placed on a properly prepared subgrade. A layer of 2 inches to 3 inches (some say as much as 4 inches) of sand, gravel or crushed stone should be compacted with vibrating equipment. “The subgrade should be well drained and have adequate and uniform load bearing characteristics,” says Cindy Rizzo, manager of training program development for L.M. Scofield Co. “It should be moist, completely consolidated and free of frost, mud or standing water.”
Porous form materials like untreated lumber or plywood can cause discoloration of the finished project because they absorb water, changing the water/cement ratio. Using form liners, epoxy or urethane-coated plywood eliminates this problem. Forms should be placed to allow uniform thickness of the slab.
Proper weather conditions are critical for good results. Mild temperatures and high humidity with no rain forecast are the best conditions. If cool weather or project changes must be accommodated, make sure to use the same mix across the job so the finished project will look consistent. Joe Garceau, president of Butterfield Color, recommends using a surface evaporation retarder in dry climates to keep moisture in long enough to allow good hydration and finish time. He cautions against troweling a surface treated with a retarder too soon, though. “If you trowel the surface while the agent is still wet, you’ll trowel water into the paste layer and alter the color,” he says.
Colored concrete should be discharged as close as possible to its final location and moved with shovels rather than vibrators to prevent separation of the components that could make the color less uniform.
Finishing
Even though integral color is consistent throughout the slab, how you finish the surface has a significant impact on the final appearance of the colored project. Wood floats are preferable to magnesium to avoid trapping moisture during bull floating.
Troweling integrally colored concrete requires extra care. “Troweling too soon potentially works bleed water back into the concrete and traps it there,” explains Grace’s Art Tyson. “Over-troweling changes the water/cement ratio at the surface and darkens the color.” Garceau agrees, adding, “Power troweling or over-troweling can burn in a finish, darkening the color and leaving the high spots darker, resulting in uneven color.” A broom or swirl finish will avoid this problem, but where troweling is desirable, workers should take care not to over-trowel.
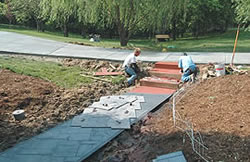
Imprinting colored concrete is an excellent technique for minimizing visual variations and covering minor imperfections. Antiquing release agents can be used successfully with integral color, but they should be applied properly to get the best imprint. “Applying too much release when stamping is basically wasting material,” explains Steve Johnson, marketing and product development, Solomon Colors. “A light dusting is all that is needed to achieve a clean release of the stamp from the concrete. An excess amount of release agent will prevent the full texture of the stamp from being imprinted.”
Curing methods have an impact on the outcome of integrally colored concrete. Calcium chloride cure accelerators cause a chemical reaction with colored concrete that will spoil a project. Rizzo recommends using a curing compound that is color-matched to the integral color and manufactured specifically to be compatible with the coloring agent. Avoid wet burlap, plastic sheeting or waterproof paper, as these will cause mottled, uneven color. Once again, consistency is key. The entire project should cure at the same rate to keep the color uniform. It is important to keep construction materials and traffic off the slab until it is completely cured to avoid causing “shadows” in the color.
“Water is a Killer in Color”
With a consistent mix, proper subgrade preparation, good weather and careful finishing, the only risk left is contractor error. Most experts agree that the addition of unwanted water is one of the most common reasons integral color projects disappoint. This can occur in many ways, including practices that are common when placing gray concrete.
Water should not be added to the mix at the site. Adding water will lighten the color and introduce inconsistency from batch to batch. Worse, increasing the water-cement ratio weakens the concrete and can lead to crumbling.
All bleed water should be allowed to evaporate before finishing. Otherwise that water is troweled or broomed back into the surface and it will change the color.
Water should not be introduced to the surface of freshly placed concrete. “There is an old finishing trick, bleaching gray concrete by hosing it off to make it look whiter by bringing efflorescence to the surface,” Garceau says. “But water is a killer in color. Using this technique with colored concrete will cause efflorescence and spoil the color.”
Another common mistake is to rinse off a broom with water and then run the wet broom over the surface. The water from that pass will lighten the color just in that spot. A better technique is to wipe off excess paste or rub it off on a piece of lumber.
Applying a curing or sealing agent too heavily can trap moisture, Steve Johnson points out. “Stripping the sealer or lightly sanding these areas will allow the moisture to pass out,” he says. “Most of these dark spots will go away naturally over time.”
Some errors can be remedied. A mild acid or scrub wash will often remove efflorescence caused by excess water. In extreme situations, texturing the surface with sandblasting removes the damaged surface and exposes the original color, but of course this results in a different finish than the one originally intended.
Color-matched sealers are used frequently for maintenance on integral color, Rizzo says. “The finished look depends on the application method. They should be applied with an airless sprayer for a more even look. The airless sprayer also lets you apply in thinner coats.”
Achieve Success With Integral Color
Attention to detail is what ultimately pays off in a successful integral color project. A few general guidelines will help you deliver a finished product that delights the customer and looks good for years.
“Consistency is key,” says Nick Paris, vice president of Davis Colors. “For best results, owners and contractors need to pay close attention to details and take extra precautions to make sure placement and finishing of decorative concrete is done consistently and with craftsmanship.”
First, manage expectations. Don’t promise an impossible outcome. Instead point out (or better yet, demonstrate) the attractive, durable, natural look integrally colored concrete can produce.
Second, be consistent. Work with the whole team to be sure the mix remains consistent, the conditions are as consistent as possible and the finishing is consistent.
Third, keep water in its place. Don’t use extra water to make the slump more convenient, to cure the concrete or to facilitate the finish. It will change the color and weaken the concrete.
Fourth, be a craftsperson. Have your crew do their best, most careful work. Errors that are overlooked in gray concrete are not easily forgiven in a colored concrete job.
Finally, get help. Ready-mix producers and color suppliers have lots of experience and it is in their best interest to share it with you.