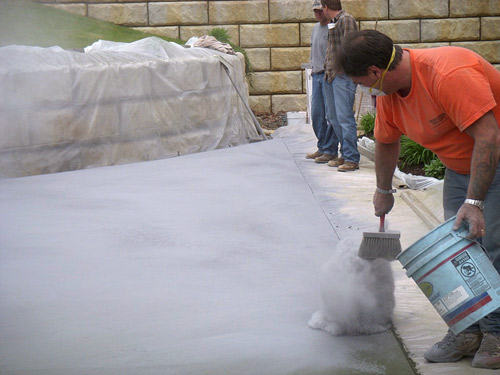
In pattern-stamped concrete work there is no alternative to using a release agent. Without one, your texture mats or texture skins will stick to the surface of the wet concrete.
The choice you have is between a liquid release agent and a dry-powder antique release. Both products are similar in function — however, the application technique is completely different for each. This results in a different final look as well.
Dry-powder antiquing release agents
The dry-powder release agent is part of the original process of pattern stamping that was done for decades. It results in more realistic-looking stone creations.
Dry-powder release provides secondary color for the project with the help of pressure. This pressure comes from the action of embedding the texture mats or skins into the surface of the semihardened concrete with the tamper.
There are a few factors you will need to be aware of while using a dry-powder antique release agent. First, it is very flighty in nature and can create one a heck of a mess.
Also, this material exhibits hydrophobic properties. Repelling water is one of the main functions of this product. It is primarily designed to provide a membrane between the surface of the wet concrete and the texture mat.
You will need to be aware of how the dry powder works with your base color. When this color is a darker shade than the base, you get the antiquing effect.
Also, be aware of what stage of set the concrete is at. When it’s wetter, the powder will cling to every contact area of the texture mats. But when concrete is starting to set, you have to pound in the texture, and the release agent will be ground into the lower areas of the pattern, such as the joints, but not be as dominant at the high points of the pattern or texture. This can be a challenge for the inexperienced installer.
So after you remove the dry-powder release agent, you will need to balance the differences in color at the points where you started and finished stamping, or at places where a summer pour was in the shade.
You should normally allow the surface to build strength for several days prior to release-agent removal, so the surface is not damaged by release agents that are removed too soon.
Damage can occur if you allow an inexperienced worker on your crew to pressure-wash the release agent off the morning after you poured. Proper dry-powder release removal is actually a major part of the final product your company will turn out. I would not recommend allowing just anyone on your crew to perform this function. The action of removing the excess release agent also leaves behind the secondary color and final look of the project.
The proper technique is to provide some agitation by mechanical means coupled with using the pressure washer. You could create score marks or a striping effect from the pressure washer alone, and usually these score marks are very hard to cover up, if not impossible.
A good way to think about the benefits of agitation is to consider the brush at the car wash. All the water pressure in the world will not clean the surface like the agitation provided by the brush. And your surface of the concrete is very porous and rough in comparison to your vehicle — there is no way the surface of your concrete will be clean without agitation to dislodge the debris.
Properly removing the excess release agent will help you reduce sealer failure. If release-agent residue is still on the surface and you seal over it, you’re setting yourself up for problems and call-backs down the road. The word “release agent” should tip you off — it makes the mats not stick to the surface, and the same will happen to your sealer if excessive amounts of it are left behind.
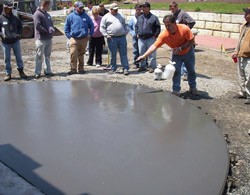
Concrete Kingdom Training Center in Pennsylvania.
Liquid release agent
The liquid release agent is a nice option where you cannot afford to make a mess or you are in a situation where the mess of pressure-washing off the dry-powder release is unacceptable. This is a common scenario at the entrance to a storefront, in a hospital or hotel, or if you plan on doing some stamping while installing indoor work.
The liquid release agent is basically a solvent that is designed to lubricate the texture mat, provide a parting membrane between the mats and the surface of the fresh concrete. High-quality liquid release agents are also pigment dispersants, so by adding pigment to this clear fluid, you can provide secondary color similar to what is provided by dry powder. Actually, most contractors add powder release agent to the clear liquid to get the secondary color.
The amount of color additions or dispersions should be figured using a combination of pigment weights
and liquid release volume. For example, you would add 2 ounces of dry powder to each gallon of fluid. This combination is mixed in a clean container, then put into the sprayer.
Always remember to shake the sprayer continuously, as the pigments will settle in the fluid. The settling helps to bring on the antique effect but can be a problem when the sprayer sits for a while. It may cause you to apply too much color.
To avoid this problem altogether, we usually instruct contractors to use two sprayers simultaneously. Use one sprayer for pigmented liquid release agent and the other sprayer for clear liquid release agent. You should move the pigmented material around on the surface with the clear spray from the second sprayer. This will allow you to balance the color throughout the area you’re working on. This should be done while you are in the process of stamping the fresh concrete, not the next day after the concrete is already hardened. With some practice you will be able to obtain just about the same look as you get using the dry-powder release agent.
When using the liquid release agent, you must wait until all the fluid has evaporated completely before sealing the slab. Using solvent- or water-based sealers over unevaporated liquid release agent will only cause you problems.
One benefit you will get from using the liquid release is faster production. There will be no need to wait days before the dry powder can be removed. Once your liquid release agent is completely dry, you can then seal the slab.
Don’t make your own
Over the years, I have seen many contractors try to make their own home-brewed concoctions of liquid release agent. Some methods work. However, the home-brewed concoctions can have some costly effects on your tools or the quality of your job.
A very experienced contractor we know once tried to save a few bucks on a large job by making their own liquid release agent. I think they used a mix of high-strength solvent and transmission fluid. Their texture skins all curled up on this project like potato chips. They ruined their tools and it cost them the entire tool set. This cost far outweighed the cost of the liquid release.
I have seen another guy use a different home-brewed method. On that job the solvents used made the texture mats swell up and hindered how they interlocked. This was another costly learning curve. I watched this guy ruin approximately $2,750 worth of texture mats.
The cost of a good high-quality liquid release agent is minimal compared to the overall expense of doing a good high-quality pattern-stamped project.