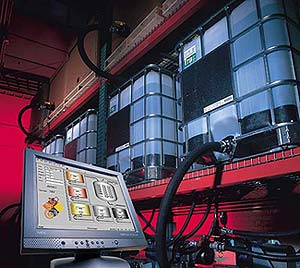
It’s finally happened: Computers and concrete do mix. And they’re mixing well, especially when it comes to integrally colored concrete.
Thanks to the technology of companies such as Solomon Colors, Davis Colors and Master Builders Inc., there are systems designed to automatically weigh out the correct amount of liquid coloring agents into a holding tank which then discharges it directly into the mixer truck. The primary components consist of a control panel, a weigh chamber and hose pumps.
“It takes about 10 minutes to train someone how to use our system,” says Nick Paris, vice president of marketing for Davis Color, a subsidiary of Rockwood Pigments headquartered in Los Angeles. “Our goal was to make it as easy to use as an ATM machine.”
The Chameleon, as Davis’ system is named, combines liquid color metering technology with the computing power of a standard PC and the versatility of a Windows operating system. Likewise, Solomon Colors’ ColorSelect liquid dispensing system and Master Builders’ CHROMIX CAM (Coloring Admixture Measuring) System operate on a Windows-based platform, with the CAM featuring touch-screen controls rather than a keyboard.
The strength of all three, proponents say, is that the dosing and mixing is completely automated, thus avoiding potential mistakes, guaranteeing batch-to-batch consistency and eliminating unnecessary labor and cleanup. Because — shades of George Jetson — all you have to do is push the button.
The color revolution
“Liquid color has revolutionized the way color is added to ready-mix concrete,” says Rich Solomon, president of Solomon Colors Inc. in Springfield, Ill. An operator simply enters how many yards will be colored, the bag mix, the name of the desired color and “the machine figures out the rest. It’s easy. You don’t have to think.” And best of all, he adds, “You’ll get the same uniformity batch after batch.”
In the United States, the demand for colored concrete is estimated at more than 4 million cubic yards per year — approximately 1 percent of total production — but that figure is expected to grow three to five times higher within the next decade. Colored concrete is being used today on everything from tilt-up concrete panels and residential sidewalks to stamped concrete creations and roadway beautification.
According to Bob Nussmeier, executive director of Master Builders Inc., a Cleveland, Ohio-headquartered company that has an alliance with the L.M. Scofield Co. to market and manufacture the liquid CHROMIX L coloring admixtures, “Throughout the country, 2 percent of all concrete is supplied with color from a ready-mix producer. We see that growing to 5 percent by 2006 because of improvements in product and dispensing technology that make it easier to supply the demand in the marketplace.”
Dry vs. wet
Although those in the know maintain that liquid and dry colors share the same physical characteristics and each can get the job done well, they admit that the dry colors take longer to disperse throughout a mixture. Because of this, Solomon explains, “There’s a potential for more streaking when the color is not fully developed. You won’t get that with a liquid added at the plant.”
And then there are the dry color bags to contend with. For starters, it’s no secret that you inevitably get little pieces of paper in the mix, no matter how much they’re pulverized. And if you rip the bags and pour, things tend to get a bit messy, the ready mix operator included. And in the course of storing and moving the bags about, the bags get wet, rip and some of the powder is lost — which translates into less color for the mix and inconsistent batches.
Finally, ready-mix plants have to have a pretty hefty inventory of dry color to produce the shades customers order. And if you want just a tad more of a certain color and they’re out of bags, you’re out of luck.
With liquid color, ready mix operators only need to have four or five primary colors — typically a yellow-tone red, a blue-tone red, a yellow and a black or two — and they can produce hundreds of different colors in quantities large and small.
“Contractors are reporting better color consistency with these systems,” Paris says. “But the primary benefit is the better availability of color. Ready-mix producers can produce virtually any color at a moment’s notice,” he adds, with the exception of the more expensive greens and blues.
But that could change as technology marches on. “We’re in the process of doing field verification and a limited release on exciting new color technologies that will dramatically expand the color range,” says Nussmeier of Master Builders.
Matches and batches
Because these new systems are much more accurate with dispensing color, many ready mix plants so equipped will guarantee color accuracy for batches as small as two yards.
Solomon says his company recommends a two-yard minimum but, “Our system is accurate enough to get good color mix at one yard.”
But, interjects Paris, “Most ready-mix companies have a minimum of 3 cubic yards.”
As for the percentage of color in a mix, “You can have too much color,” Paris continues. “The intensity of a color rises to a certain level and gets maxed out,” somewhere around 7 percent to 8 percent. “If you go past 8 percent, the color starts displacing the cement and it can reduce the strength of the concrete,” without intensifying the color. “Typically, most color dose rates are 5 percent or below.”
Solomon, who says most of his company’s formulas go as high as 4 percent, adds that operators would have to manually override the software on the new coloring systems to make the percentage go higher. “Theoretically, it’s not going to happen.”
The color load can go as low as .5 percent, he adds, but he recommends the percentage be 1 percent or more to achieve uniform color.
Adding color at the plant shouldn’t have any adverse effects on the concrete, all three men agree, as long as the percentage is around 4 percent to 5 percent and the slump 4 inches or less.
The bottom line
For the ready-mix producers, these integral coloring systems cost in the neighborhood of $40,000, depending on the options selected. There are several ways to obtain a system, including buying it outright or over time with a surcharge added to the color agent or material purchased from the manufacturer of the machinery.
“In ready mix plants, truck time is money,” Solomon says. With these systems, “you can batch out colored concrete just as fast as gray concrete” with a much healthier profit margin. As far as installation labor, integrally colored concrete is less intensive than other decorative techniques.
ng on whom you ask and what part of the country you’re in. The colored product is no more complicated to install than plain gray concrete but, cautions Paris, purchasers of colored concrete have higher standards of appearance then purchasers of uncolored concrete, so contractors need to raise their level of workmanship to meet increased expectations.