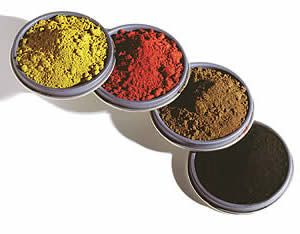
Pigments are finely ground colored particles that, when blended into a concrete mixture, infuse the concrete with their shade. Humans have been using pigments since Paleolithic times, when pulverized minerals and charcoal were employed in cave paintings that have retained their vivid coloration for as many as 30,000 years. While today’s pigments contain some of the same mineral oxides and carbon black compounds our ancestors used, synthesized pigments have substantially replaced pigments refined from naturally occurring mineral deposits. The new processes have resulted in pigments that have greater tinting strength and are more consistent and economical to use.
Not just any pigment can be used in concrete. The alkaline chemistry of portland cement plus long-term exposure to sunlight and weather can cause all but the most inert colorants to fade. In addition, concrete colors have to be wettable so they can disperse readily throughout a concrete mixture. And pigments must not interfere with the workability or structural characteristics of concrete. ASTM C979 — Pigments for Integrally Colored Concrete summarizes these requirements and should be the basis for colored concrete specifications.
Color concepts
Pigments should not be confused with “dyes”; while both are colorants, pigments are insoluble whereas dyes can dissolve and are not suitable for concrete. The optics of pigments are based on the spectral characteristics of light. When exposed to light, pigments create color by absorbing certain frequencies of the visual spectrum and reflecting others. Red pigments, for example, absorb blue and yellow light and reflect light at the red end of the spectrum.
In addition to color or hue, pigments also differ in tint strength, the relative ability of a pigment to impart color. For example, it could take ten pounds of a low tint strength pigment to equal the color achieved by just four pounds of a pigment with high tint strength. Taking this into account, a pigment with low cost per pound but low tint strength may be less economical than a somewhat more costly pigment with higher tint strength.
Designs for colored concrete mixtures include a pigment dosage rate expressed as the required weight of pigment per “sack” of cementitious material or, sometimes, expressed as a percent by weight of the cementitious material. Cementitious material includes the weight of cement, lime, fly ash, and other pozzolanic or supplementary cementitious materials in a mixture, but not the aggregates or water.
Dosage rates as low as 1⁄2 pound per sack of cementitious material can have a pronounced impact on concrete, creating subtle shades that harmonize concrete with other building or landscaping materials. Increased dosage rates create more intense colorations. Above a certain dosage rate, however, pigments achieve color saturation and the addition of additional pigments will not intensify color. While the saturation rate of colored concrete varies with the pigments used, most high-quality pigments achieve saturation at dosage rates of about 5 or 6 pounds per sack of cementitious material. This is well within the 10 percent dosage rate limitation imposed by the ASTM standard; higher dosage rates could affect the strength and water/cement ratio of concrete.
While pigments have the most conspicuous impact on concrete color, other factors must be considered. Portland cement, for example, comes in a wide range of shades — from gray or buff to white — that darken or lighten the overall appearance of colored concrete.
Aggregate color is also a consideration. As cast, a thin layer of colored cement paste covers aggregate particles. When aggregates become exposed — deliberately due to sandblasting, abrading or other finishing processes or because of wear and erosion of the concrete surface — the aggregate’s color combines with the color of the cement matrix to create the overall appearance of the concrete.
Mixtures with high water/cement ratios will appear paler than mixtures with less water. The texture of a concrete finish impacts color, with broomed or other rough surfaces appearing lighter in color than smooth trowel or form finishes. Note, too, that rough textures can often minimize the visual impact of
minor blemishes in concrete. Finally, concrete lightens in color as it cures, so samples or installed work should be allowed to cure 28 days prior to making final evaluations of appearance.
Pigment choices
The pigments most widely used in concrete are mineral oxides, particularly iron oxide, the same compound known as “rust.” While we typically think of rust with a reddish orange color, there are actually several variations of iron oxide, each with their own hue. These include: red iron oxide (Fe2O3), yellow iron oxide (FeOOH) and black iron oxide (Fe3O4).
This palette is expanded by chromium oxide (green) and cobalt oxide (blue). These pigments are significantly more costly than iron oxide and increased care must be exercised when handling them due to health risks associated with long term exposure to heavy metals.
Titanium dioxide, a white pigment, can be used in concrete but has limited application since it is generally more effective to brighten concrete with white portland cement or white pozzolanic materials such as high reactivity metakaolin.
Carbon black, the pigment found in soot and charcoal, is an economical black colorant with high tint strength. Ordinary carbon black pigments can leach out of concrete exposed to repeated wet/dry cycles unless the concrete is well sealed; the same problem can occur in browns and tans blended with ordinary carbon black. New formulations, however, have resulted in carbon blacks that bond permanently in concrete. Carbon black can interfere with air entraining admixtures and requires special consideration when used in freeze-thaw conditions.
A broad spectrum of concrete colors can be produced by blending these “primary” pigment colors. For example, blending yellow, red and a hint of black creates tans and buffs. The shades available for integrally colored concrete are generally considered earth tones; this should come as no surprise since the pigments used in concrete are some of the pigments used throughout nature to color rocks and soils.
Naturally occurring pigments, such as ochre, umber and natural iron oxide are used primarily for reds and browns with low tint strength.
How pigments are made
The chemical engineering used to synthesize pigments is beyond the scope of this article. It is interesting to note, however, that the feedstock for the manufacturing processes includes recycled iron and steel from post-industrial sources. This makes colored concrete compatible with sustainable construction practices such as the Leadership in Energy and Environmental Design (LEED) program.
Optimum tint strengths of mineral oxides are achieved when pigments are ground to a fine powder ranging from .05 to .10 micron diameter. This is about one-tenth the size of typical portland cement particles and small enough to get permanently bound into the interlocking crystals of hydrated cement. Powders are available in bulk or a variety of package sizes. For ready mix applications, powders are can be packaged in repulpable paper bags that can be tossed unopened into mobile mixers to simplify handling, reduce dust, and eliminate the need to dispose of empty bags.
Increasingly, pigment producers are processing powder pigments into granules or liquid slurries that are compatible with automated color metering systems. Granules are used extensively to produce concrete masonry units and other zero-slump concrete products where very low water/cement ratios are required, and liquid colors are rapidly gaining acceptance among ready mix concrete producers.
Powders are typically factory-blended to create a color producer’s standard shades or custom colors. Automated systems, on the other hand, typically use just a few primary colors (e.g., the various hues of iron oxide) to blend the required shade at the concrete producer’s plant. In the same way that paint stores offer their customers an almost unlimited range of options by mixing colors on demand, the automated systems offer many benefits: Contractors are assured of getting the color they need
without worrying if the concrete producer has a particular blend in inventory. Designers get to select just the shade they want without being limited to the options on a pigment manufacturer’s color card. Concrete producers reduce labor costs associated with manual coloring. And everybody benefits from better quality control since the chances for human error are reduced, colors are added at the same time in every batch for consistent mixing time and greater batch-to-batch uniformity, and the automated systems prepare batch tickets showing precisely the colors added.
Using pigments
PCA offers guidelines for successfully placing, finishing and curing colored concrete, and PCI offers a helpful set of color prints showing the appearance of many colored concrete finishes. Pigment producers are also an excellent source of design ideas for and technical information about colored concrete.
When mixing colored concrete on-site, ingredients must be placed into the mixer in sequence to assure pigments disperse fully. With powdered colors, put pigments into the mixer along with aggregates and approximately half of the required water and then mix; follow this by adding cement and sufficient water to obtain desired consistency or specified slump. With liquid colors, place approximately half of the required water into the mixer, add pigments and mix; then add dry ingredients and mix while adding the balance of required water.
Pigments for integrally colored concrete should not be “dusted” onto the surface of concrete. Dust-on colors or “color hardeners” are preparations of cement, fine sand and aggregates blended with pigments so they become monolithic with the concrete surface.
Concrete is a natural material and subject to mottling and color variation whether pigmented or not. Before construction, take the time to make sure designers and building owners have realistic expectations about the appearance of a proposed project. Final selection of pigments should be made after viewing properly cured samples or mock-ups produced with the materials and techniques proposed for the project.
Following these guidelines will help assure that the colored concrete designs you create are as functional and durable as they are beautiful and inspiring.