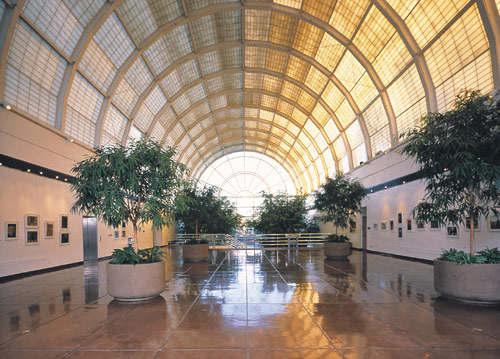
Restoration projects done properly allow contractors to make fixes and changes that blend into the existing floor instead of standing out like a repair. Also, stained concrete sometimes needs to be refurbished. Finally, when it comes to colored concrete, why not maintain it?
There’s no argument that refurbishing colored concrete is less expensive and disruptive than ripping it out and replacing it.
“One advantage to a color restoration project is that superficial imperfections may be corrected during the restoration phase,” says Scott P. Thome, director of product services for L.M. Scofield Co., a full-service manufacturer of concrete materials. “Maybe by changing the sealer the project will have a longer service life.”
Restoration projects done with the proper products allow contractors to make repairs and changes that blend into the existing floor instead of standing out like a repair, says Peter Wagner, vice president of marketing and product development for AmeriPolish, which specializes in polished concrete products.
Restoration also gives property owners a second chance to maintain the floor properly if they hadn’t been doing a good job before.
Using the proper products to restore a floor is essential. “As far as going back and adding color [to a polished floor], using dyes is really the only way to do it with consistency,” Wagner says. “And before we had our penetrating agent, we couldn’t always get the penetration of color we were looking for. We would have to regrind, dye and repolish. Now we can often add color without having to redo the whole thing.”
Restoration projects can be time-sensitive and closing a business to restore a floor is very costly. That fact is what makes Newlook water-based stain so popular and well received. The stains were developed to fix common problems such as discolored, wrongly colored, blotchy or badly stained concrete, as well as to maintain colored concrete surfaces.
On a typical driveway, says Newlook International Inc. president and CEO Reid Langston, you can pressure-wash the surface, apply two coats of Newlook stain and be done by noon. People can walk on the surface two to four hours after the job is done.
Using this stain is also great for residual business, he adds. He has one client who has him touching up a surface every six months to keep it looking pristine. “Contractors can go over it again and again without it costing the customer an arm and a leg,” he explains.
However, one of the disadvantages of his product, he admits, is that if you use patch material, the different texture will show. The stain doesn’t change the texture of the surface and it won’t fill in any cracks.
Before accepting a restoration project, you should have knowledge about the project and experience with the product you plan on using, advises Thome. “Look into why the restoration is taking place and determine what the owner wants in the end. Sometimes these expectations do not match up.
“Developing skills to alter and enhance another contractor’s work is challenging. Having a good understanding of color development is a skill that comes from experience. Training seminars do not give you enough information. Placement techniques can be taught but that’s not enough. To restore a project is not just covering it up. It is working with what is there and then providing a solution that owners can accept within their budget.”
On the road to recovery
Sometimes, the problem with stained concrete is that the sealer or wax has become dull, while the surface below remains abrasion-free, says Sherry Boyd, director of marketing for L.M. Scofield Co. “In this case, the sealer can be stripped off and the surface resealed carefully following the manufacturer’s technical information.”
Other times, she says, the concrete needs to be restained or resurfaced. Either way, the surface needs to be prepared before any work is done. If you’re restoring a floor, it’s best to talk to the manufacturer of the products used to color, seal and texture the concrete to determine if it’s best to use a power wash, a coating remover or even a grinder to get down to clean concrete.
Boyd believes it’s very important to seal interior and exterior stained concrete in the first place, typically using a roller or an airless sprayer. After they’re sealed, interior floors should be regularly waxed with a maintenance product, she says.
Langston says his products used to restore color don’t need sealers, although they are compatible with them and contractors could offer sealer as an option. “That’s a big selling point,” he says.
![]() |
![]() |
Maintenance is key
All this said, when it comes to colored concrete, an ounce of prevention is worth a pound of cure. So why not maintain it?
“When property owners select colored concrete there is an expectation that the appearance of the surface will be clean, neat and protected per the installation specifications or manufacturer’s recommendations,” says Harry Moats, president of L.M. Scofield Co. “The beauty and color intensity won’t last unless the surface is properly maintained.”
Like other surfaces in or around a home, routine maintenance is required to keep colored concrete fresh and new-looking.
“We don’t hesitate to clean and wax the kitchen floor when it gets dull, scratched or dirty,” Moats says. “So why won’t we do the same to our decorative concrete? This is a small price to pay to keep that new, fresh and clean look that we started with. Contractors need to communicate to the property owner about the need for regular maintenance.”
Wagner agrees. Any polished concrete surface should have a maintenance program, he stresses, whether it’s wet mopping or auto-scrubbing. Dirt particles grind down the finish, open up the floor to further abrasion and cause the surface to wear faster. Keeping the surface clean with the right agents will prolong its life. Sulfates and hydroxide, which attack and degrade concrete, can affect the polish and dull the floor.
A good walk-off mat system is also a must for a floor’s longevity, as it acts as a sink for soils and dirt, Wagner adds. But it’s still necessary to clean and maintain the mats.
Maintaining a pristine look is high on the list with many residential customers who are concerned about curb appeal, says Langston of Newlook, but it’s especially important for commercial applications. “It projects a good-looking image if the concrete is maintained, and that’s very important to such places as restaurants, supermarkets and theme parks.”