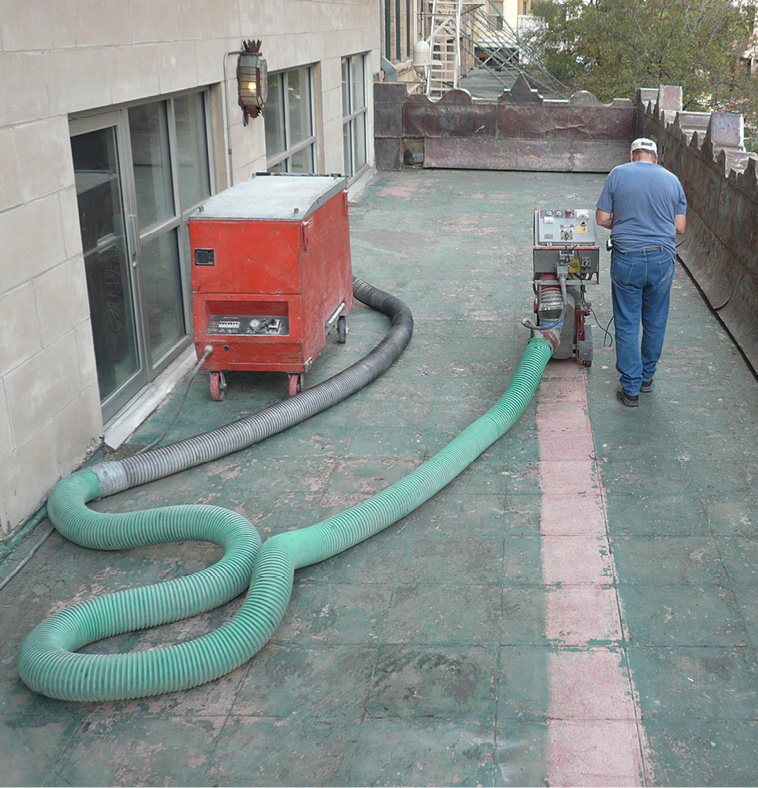
With today’s ever-changing technology, it’s critical to stay on top of your options to achieve the concrete surface profile (CSP) recommended by coating manufacturers and to choose the right equipment for surface preparation.
CSPs and common sense
Knowing the CSP you need to achieve is a very critical first step in choosing the right equipment for surface preparation.
Developed by the International Concrete Repair Institute, the CSP measures the average distance from the peaks of a surface to the valleys. It ranges from 1, which is nearly flat, to 9, which is very rough. Typically, the thicker the coating, the higher the CSP needs to be.
Bill Young, owner of Professional Construction Products in Sandy, Utah, notes that most products have a recommendation anywhere from a 2 to a 5 CSP. However, he says common sense also needs to be applied.
“I’ve seen an epoxy manufacturer say in order to put its 100 percent solids epoxy down you’ll want a CSP of 3,” he says. “In the same breath, they’ll say if you’re going to recoat an existing epoxy to sand it first, but sanding may give you a CSP of 1.
“What you need to do is know your products,” Young adds. “You need to know the state of the concrete and how strong it is. You want to do a Mohs hardness test and in some cases you’ll need to do a pH test.”
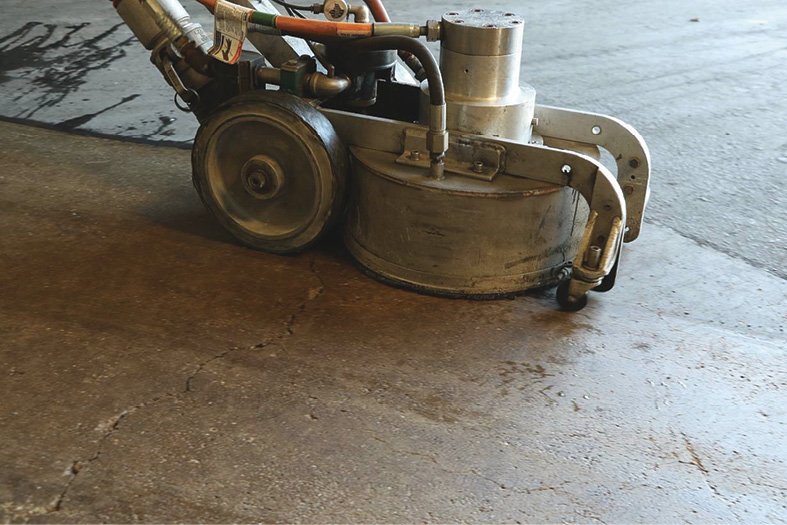
The bottom line, he says, is you need to open your concrete because the better it’s opened, the better the coating is going to stick.
When a job requires a high CSP, one of the best options for obtaining that is to use a scarifier or milling machine. The bottom is armed with multitipped cutting wheels that rotate at high speeds to chip away a concrete surface.
Because the cutting wheels are interchangeable — and on most machines come with adjustable depths — there’s something that will produce just about any type of profile needed in widths from 2 or 3 inches all the way up to 16 inches.
Young says, for instance, if he was doing an industrial room where heavy equipment was serviced, he’d use a scarifier that would give him a CSP of 10, “because that’s an insurance policy.”
And, Julio Hallack, owner of Concrete by Hallack in Turlock, California, says he would use a scarifier on any resurfacing job where the material will be more than a quarter-inch thick.
Shoot ’em up, grind ’em down
Where a more modest CSP is needed to do the job, a shot blaster or grinder will probably be the ticket. They each have their supporters, and some of the choices may come down to individual preference and what equipment is available.
A shot blaster is a self-contained wheeled device designed to throw steel shot at the bare concrete or coated surface at a high speed. By containing the shot in a blast chamber, the shot is recirculated while any dust, dirt or coatings are separated out.
Units range in width from 4 to 32 inches, and the size of the shot used and the speed at which the machine covers an area determine the rate of production. They’re not particularly effective on thicker coatings, such as urethanes, because the shot will simply bounce.
One big drawback with shot blasting, according to Rick Watson, owner of Surmac Inc. in Schertz, Texas, is that it requires a fair amount of skill.
“You can do more damage than good because if you don’t know what you’re doing you can leave overlap lines,” Watson says. “If you’re going to go back with a thin film coating, you’ll be able to see those lines and it can be a real nightmare.”
While he agrees that a shot blaster can be great to use with some jobs, he advises hiring a company that specializes in shot blasting rather than buying the equipment.
An alternate solution is to use a grinder. Grinders use horizontal disks, often embedded with diamonds, that rotate over concrete to be prepared. Machines range in size from single-disk walk-behind units to triple- and quadruple-disk ride-on machines for high production.
Both Watson and Young say they’re a pretty common solution to many prep problems. However, Young says, as with anything else, the job has to be done right.
“You have to use the right diamonds, but you also have to clean the concrete very well when you’re done and make sure there’s no dust,” Young says, as dust can be a real bond-breaker.
He cautions against putting grinders with scabbler heads in the hands of untrained crew members as the heads can pulverize and damage concrete.
Of course, the secret to success with a grinder is using the right diamond tooling, Watson says. And, even if you’re using another method to prep most of your surface, Hallack notes, a grinder is a good tool to have on hand.
“Almost any surface prep job will require grinding next to walls, equipment, toilets or any type of furniture that cannot be removed,” Hallack says. “It’s very commonly used along with a shot blaster to do the areas that the blaster cannot reach.”
Water and chemicals
Mechanical methods for surface prepping aren’t your only choices. Both Hallack and Watson are sold on what Watson calls “ultra-high water-jetting,” which uses water under pressures up to 55,000 psi (pounds per square inch) to prep not just concrete, but other surfaces, as well.
“It’s one of the best technologies, if not the best,” says Hallack. “It can be used in any type of surface prep. It’s very clean, there’s no dust and hardly any water is left on the surface.”
“It can be used for removing virtually any of the coatings on concrete, and also to scarify the concrete at the same time,” says Watson. “Or, they can be adjusted pressure-wise to only remove the coating and not damage the concrete, or lightly etch the concrete in preparation for a new surface.”
However, both men acknowledge that — like shot blasting — the equipment requires more than a little skill to use. And, it’s also expensive, which is why both recommend subcontracting the work out to a company that specializes in high-pressure waterjets.
Chris Finegan, owner of Green-Tec Services in Orange, California, a company that does such work, says besides being able to adjust the water pressure to exactly what’s needed, the process leaves zero dust and the water is contained and reclaimed, as well.
“It’s often specified due to the benefits it offers in interior environments during occupied remodels, as well as for the health considerations of the operator and those around the work site,” Finegan says. “And, it’s also one of the fastest methods in the industry. It’s possible to do upwards of 20,000 square feet in eight hours with one machine.”
Still another option is to use a chemical prep, Hallack says, particularly if an acid or color stain is going to be applied over concrete that’s previously had tile, vinyl or carpet on it. A chemical stripper can be a good choice, he notes, recommending those made by Jasco.
“The glue or grout has to be removed very carefully,” he says. “That can be done using something that will soften it up and then removed using a scraper. It’s meticulous and challenging, but it can also be done fairly quickly.”
It’s also an approach that works on new sites where other subs may have used pencil or markers on the concrete, or to clean up overspray from the painters. The key is making sure the surface is then washed clean using a scrubbing machine.
“In jobs like this, you want to protect the surface of the concrete as much as possible,” says Hallack. “And, you don’t want to expose any of the aggregate; you don’t need to open it up. And, remember to protect the walls, doors and cabinets. It will save you a lot of money.”
In short, there is no one best method for doing surface prep, and the easiest way to ensure a successful job is to reach out to others who have already gone through the hard steps to learn what works best.
“You can call somebody like me to help, but the equipment manufacturers will also field calls, and the diamond manufacturers, and the coatings manufacturers,” says Young, who often serves as a consultant. “There’s no reason for a bad prep job, but be proactive and not reactive. Call before you start, and not after the floor starts to delaminate.”