Winning the battle with Mother Nature becomes a little challenging when the weather heats up. This is also the same time our services are in highest demand. There are ways to combat the heat and the challenges it creates, but few are profitable. You can lessen the amount you pour (not profitable). You can hire more hands (not profitable). You can take vacation until the weather breaks (definitely not profitable). I’m proposing something that doesn’t require more hands or less footage poured.
I was surprised the other day when I swung into our local concrete supply house to pick up a product that I assumed everyone was using. This supplier specializes in products for decorative concrete tradesmen, so it shocked me when I asked for an evaporation retarder and was told few other contractors used this product. Now I’m not sure how many of our readers use “film” retarders, but if you aren’t, you are really missing out on something our crew wouldn’t live without. Let me explain.
An evaporation retarder is a spray of film that is applied to the wet concrete surface shortly after placement. The idea here is for the film to help hold moisture into the surface so elements like wind and sun will not dry out your future work of art. The film creates a barrier that the wind finds harder to penetrate, and this keeps your surface in a more plastic state. I won’t bore you with why this product works but I’m here to tell you it really does. If you are pouring decorative concrete you owe it to yourself to give it a try.
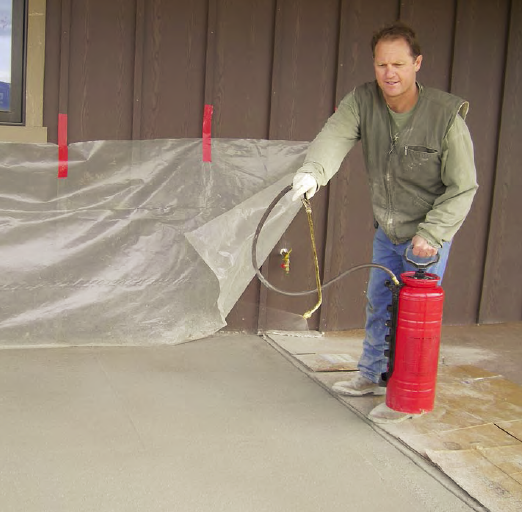
The benefits
This is a business of eliminating as many potential problems as possible. The more water your concrete has in it, the greater chance of problems like cracking, shrinking and low strength. Using a retarder allows you to pour drier concrete without the challenges of typical dry concrete, even on hot days.
The temptation on hot days is to dump water into the mix to create an easier lay-down. Many have the false assumption that this will create a longer window to create the decorative surface desired. This is not true. In actuality, using a spray-on retarder over dry concrete will create a wider window for decorative practices.
Many contractors find themselves coloring concrete surfaces with color hardeners. This type of coloring is extremely effective but can compound the drying process of the concrete surface. Some contractors stay away from this coloring type for just this reason. Adding a dry powder to an already drying surface just doesn’t make sense to these folks. The counter to this process is applying a film of retarder directly over the broadcasted color hardener. The color will work into the surface, edges and scoring with ease regardless of outside elements like wind and sun. This film can be sprayed through a pump-up sprayer several times during the drying process. The product comes in concentrate form, so it can be mixed as needed without adding much expense.
Also, a common complaint with air-entrainment admixtures used in freeze-thaw areas is the spongy feel of the surface as it dries. Using a film retarder will help with this situation. And I have not noticed any conflict between the film and color or sealers.
When retarders are used, I have noticed more consistency in imprinted concrete, especially with interlocking patterns. This is attributable to the surface moisture that is maintained via the retarder. No doubt this film applied to the drying concrete will assist in the curing process. Many new contractors stumble over the “stress fractures” or surface cracking that comes from tearing the concrete surface as it’s imprinted. This type of cracking is not good on the eyes and will have you answering questions from your customers. Use of a spray retarder will greatly reduce this type of surface cracking by trapping more moisture into an imprinted surface. Using less aggressive or deep stamp tools will help as well.
Stop by your local supply house and pickup a gallon for your next pour. You won’t be disappointed. The goal here is affordable ways to provide quality concrete for your customers. Please let me know how these products and practices work for you.
Use these links to find out more about three common retarders:
Confilm by Master Builders
www.basf-admixtures.com
Brickform Evaporation Retarder
www.brickform.com
Bonway Evaporation Retarder
www.bontool.com