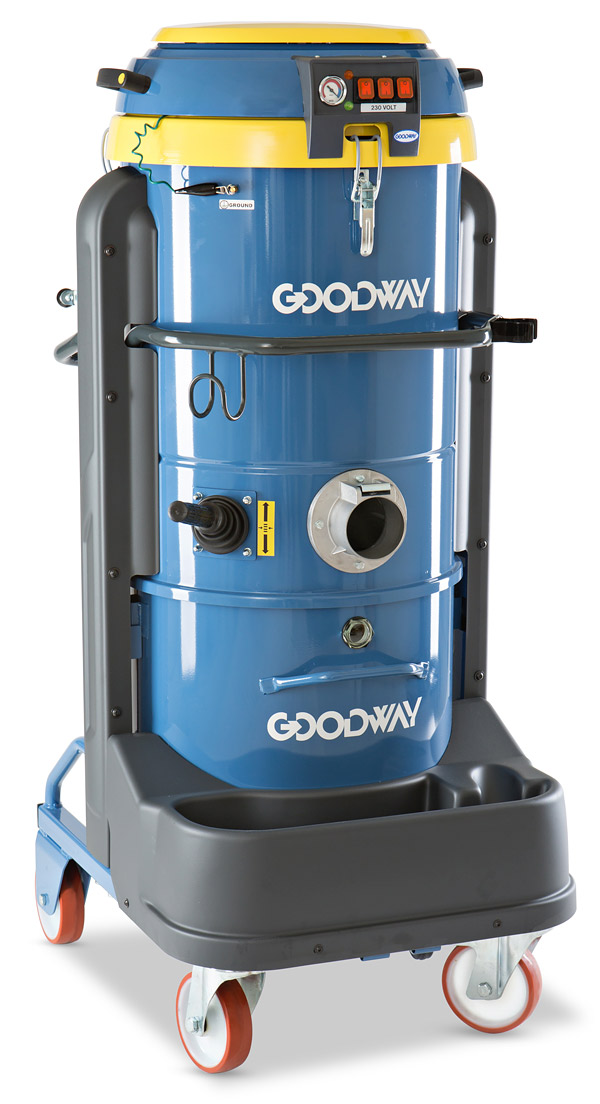
The philosophy behind purchasing industrial vacuums for controlling airborne dust is changing in the concrete industry, especially with new federal rules now in place concerning worker exposure to these particles (see sidebar).
The industry’s top manufacturers of dust-collecting vacuum systems are more than capable of helping folks meet regulations, advising what equipment is best for a job, and providing top-notch warranties, customer service and training.
What’s needed now is for equipment buyers to start thinking of vacuum systems as vital pieces of equipment, not just accessories to attach to other tools.
“Many contractors think of industrial vacuums as commodity items, available at their local supply store and quickly chosen from the limited selection on a shelf,” says Tim Robb, vice president of marketing and strategic business development for Goodway Technologies. “But, the right industrial vacuum is an investment in your business and will become an invaluable part of your tool set. A vacuum should be considered a capital expense and treated as such.”
“When it comes to deciding on a vacuum, we’re sort of the afterthought,” adds Lyndon Kelsey, North American sales and marketing manager for Ermator USA. “Customers make a decision as to what tool to buy first and then look for a vacuum that fits that piece.”
But, he adds: “We’ve always been specifically about the dust.”
Buying considerations
Dust-collecting vacuums used in the concrete industry for dry applications should have both primary and high-efficiency particulate arrestance (HEPA) filtration to contain fine particles, says Marcus Turek, Sase Co.’s North American sales manager. “This is a must and a standard within our industry. Any vacuum is only as good as its filter system.”
Before making a purchase, Turek suggests asking manufacturers how many square feet of filtration a vacuum has and how long its filters typically last.
According to William C. Vain, director of sales and marketing for Dustless Technologies, the amount of flow or suction a vacuum produces is also an important factor. He recommends vacuums with at least 120 cubic feet per minute (cfm), which his company’s products have.
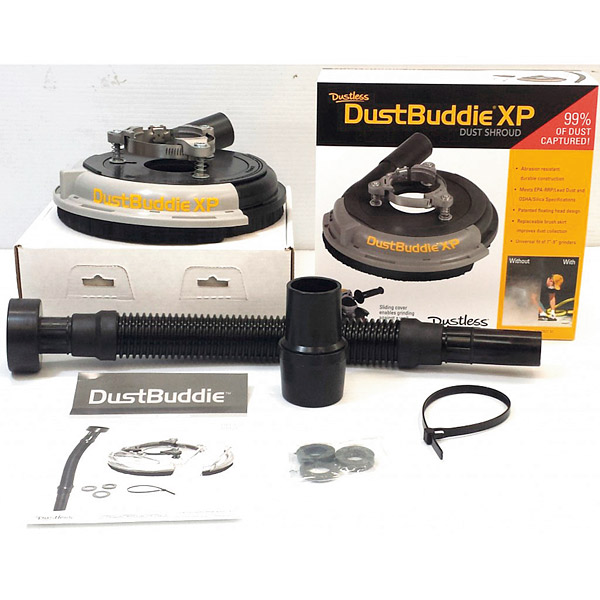
“Dustless Technologies utilizes a primary filter made of proprietary material which protects the HEPA filter from direct exposure to small particulates,” Vain says. “Each Dustless HEPA filter is tested, validated, and serialized for 100 percent material and production process traceability.”
All Ermator vacuums come with a HEPA filter to trap fine particles, prefilter to collect medium to heavy particles, and cyclonic filtration to move all particles into a drop-down bag system called Longopac.
“By turning the vacuum off, all dust falls into a bag,” Ermator’s Kelsey says. “Then, you zip-tie the bag, turn it and dispose of it. There’s no tank to empty or barrel to drop down, so no dust to clean up,” he adds. “You have to bag the dust anyway, so Longopac is the most efficient system. Simply dispose of the bag in any construction dumpster.”
Dustless Technologies also offers a micro prefilter bag that attaches to the port of its products within the barrel. The bag, which can hold up to 40 pounds of concrete dust, serves as an additional filtration device.
Goodway’s DV-E3 model industrial vacuum offers a filter shaker and large filter area to reduce filter clogs, which are often an issue for standard vacuums, notes Robb. “Our DV-E3 model also offers wet cleaning performance with a 27-gallon detachable tank.”
Sase’s Turek says it’s vital to select the right size vacuum for the equipment it will be used with. “You can never have a vacuum that is too big and powerful, but you can definitely have one that is too small,” he says. Vacuums that are too small result in excess debris left in the workplace, increasing clean-up time and costs.
“It’s important to network closely with an equipment vendor to make sure you’re using appropriately sized and priced dust-collecting vacuum systems for your processes,” says Turek.
Robb agrees: “Many times, choosing the most versatile vacuum may not be the right choice. Almost always, application-specific vacuums — with the right combination of cfm, lift, filtering and capacity specifications — are the best choice.”
Power and price considerations
Today’s dust-collecting vacuum systems are powered by electricity, gas, compressed air and propane, with electric models the ones most commonly purchased. Gas-powered units tend to be very costly and are mostly designed for outside use.
Dustless Technologies, Vain says, offers units that incorporate dual motors, which operate on a 120 circuit or a 240 circuit.
At Goodway, the vacuum voltage requirements run from 115 to 480 volts for very large systems, but most users opt for models that operate on voltage between 115 and 230. This company, as well as Ermator, offers vacuums in a range of international voltages.
According to Robb, Goodway’s compressed air-powered units are good for picking up powders because of their high cfm specifications. However, he adds, compressed air units aren’t as strong for cleaning wet materials.
Sase’s Turek says propane vacuum units are becoming popular for use with propane-powered planetary diamond grinders and polishers. “All propane equipment used indoors that Sase sells have emissions purification systems on them to aid in minimizing exhaust concerns,” he says.
Kelsey notes that his company’s products are a “premium line,” but because Ermator is one of the largest HEPA construction vacuum manufacturers in the world, its products are “very price-competitive and cost-effective.”
Vain says Dustless Technologies’ contractor-grade units that offer HEPA technology and elongated life cycles begin at $400 for small capacity 10-12 gallon items. Options, such as explosion proofing, drive prices higher. He adds that general contractors looking for a vacuum with superior, proven performance, durability and long life-cycle can expect to pay at least $500. For large-scale construction projects, appropriate vacuums top $2,500.
Goodway’s vacuums that include filtering, filter shaking and specialized designs range from $2,500 to $3,500. Sase’s 110-volt systems for edge work and small walk-behind equipment typically sell for between $500 and $5,000. For containment systems for larger equipment, Turek says Sase’s price point varies between $8,000 and $14,000.
About three years ago, Ermator introduced a propane vacuum that fits the bill when a job site has no electrical or generator access. “That unit keeps up with the biggest grinders,” Kelsey says.
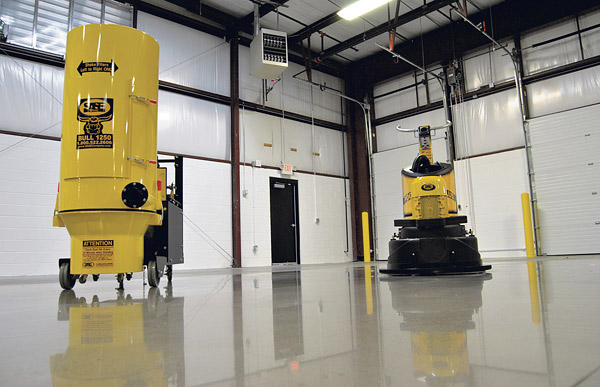
The extras
Warranties, availability of replacement parts, trouble-shooting and maintenance assistance, and training should be an important aspect of equipment selection, and these factors vary among industrial vacuum manufacturers. For example, Dustless Technologies offers a lifetime warranty on structural components and three-years on electrical items, and Ermator offers a three-year warranty on all products.
But it’s the availability of parts that these companies say is the most important to their customers. Ermator products are sold and serviced out of its Tampa, Florida, headquarters and throughout its distribution network. Sase ships all orders the same day they are received and stocks all consumables for the equipment it manufactures.
The most-needed replacement parts, manufacturers say, are filters, switches, fuses and connectors.
“Having replacements on hand is always a good idea,” Robb says, adding that most of Goodway’s filters are reusable and can last for many applications. “As with any high-performance tool, regular cleaning, inspection and replacement of working parts will prolong their life.”
According to Vain, keeping filters clean and free of debris helps protect the life of vacuums.
“What can breakdown long-term on a vacuum is the motor,” notes Kelsey. “But our motors are protected by those filters. That’s why we give the long warranties we do.”
To help customers stay on track with maintenance, Ermator includes schedules in all product manuals. Also, when a customer goes to Ermator’s website to register a purchase, a three-year extended warranty automatically goes into effect on the product.
Kelsey calls his company’s 200-plus distributors, who are extensively trained to offer trouble-shooting and maintenance assistance, the “first line of defense for the end-user.” Ermator also has a 24/7 technical hotline customers can call for assistance.
And while Sase offers six formal training classes per year at its Knoxville, Tennessee, facility on grinding and polishing concrete floors, it also has 22 staffers available around the country to visit job sites for training on all equipment and containment vacuums it sells and manufactures.
“Some things in our industry simply can’t be taught in a classroom,” says Turek.
Currently, Dustless offers a video library of training programs on its equipment and in 2017 will launch “Dustless University,” a training and education program. Courses will cover product reviews, equipment training, operational tips and OSHA compliance, Vain says. Under the Dustless University program, the company will also conduct and host webinars and compile a library of industry resource materials, all to be available on the company’s website.
“We’re excited about what this program could mean for our customers in the future,” Vain adds.
New OSHA Silica Rule Now in Place
The Occupational Safety and Health Administration (OSHA) has instituted a comprehensive new silica rule, effective June 23, which will be phased in among various industries through June 23, 2018.
Its purpose is to curb the incidence of silicosis, a disabling and sometimes fatal lung disease in workers exposed for long periods of time to elevated levels of respirable crystalline silica (RCS). OSHA estimates about 2.3 million workers in general industry, maritime and construction may be affected by RCS, including those who work with concrete products. RSC is often referred to as the new ‘Black Lung’ disease.
The construction industry has until June 23, 2017, to comply with most of the new regulations and general industry has one additional year to comply.
The OSHA regulation cuts permissible exposure limit (PEL) to 50 micrograms per cubic meter of air averaged over an eight-hour shift for workers in all industries. This is about half the previous level for general industry and about one-fifth the PEL in construction. Also, employers in general industry now must measure silica levels if their workers may be exposed at or above 25 micrograms per cubic meter.
OSHA’s regulation also outlines requirements for exposure assessment, methods for controlling exposure, respiratory protection, medical surveillance, hazard communication and training, and recordkeeping. In the construction industry, employers have two alternatives to control worker exposure: choose an approved dust control method or measure workers’ exposure and then develop dust controls based on exposure results.
OSHA estimates that the new regulation will save more than 600 lives and prevent more than 900 new cases of silicosis a year.
When announcing the rule in March, OSHA Chief David Michaels said, “Today, we are taking action to bring worker protections into the 21st century in ways that are feasible and economical for employers to implement.”
Learn more at www.osha.gov.