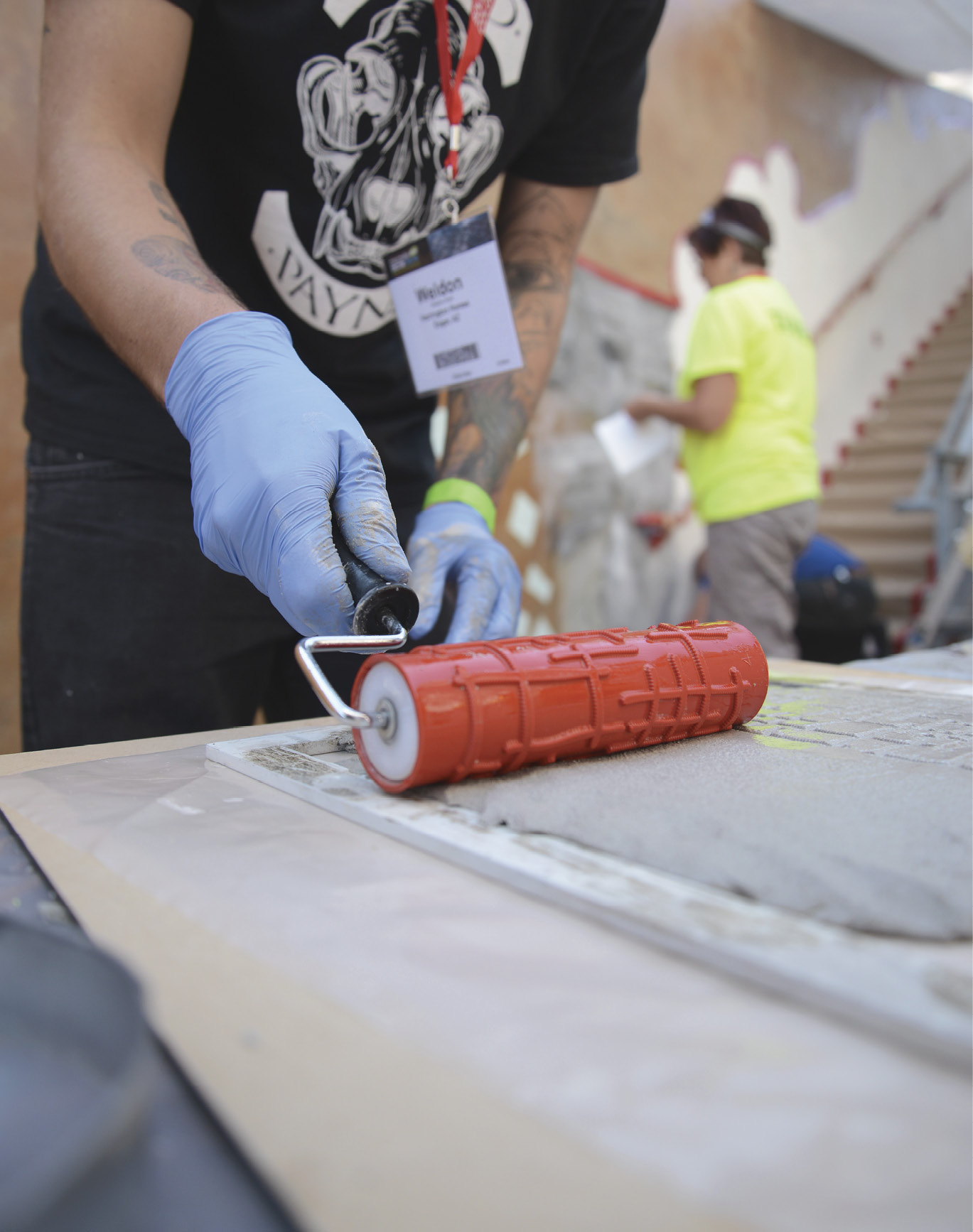
In this world, there are two types of concrete: concrete that’s flat, gray and utilitarian, and concrete that’s been shaped, colored and/or textured — and is considered art.
As art, it requires a fair amount of skill and patience to complete the transformation. Fortunately, for those inclined to add texture, there’s also a wide range of tools available that, with some mastery, can take either horizontal or vertical concrete from dull to fantastic.
Welcome mats
Ask concrete tool manufacturers the first texturing method they recommend newcomers master, and the answer is almost uniformly seamless skins.
“They’ll want to know seamless skins,” says Tyler Irwin of the Oceanside, California-based Proline Concrete Tools. “They’re the quickest, easiest way to impart a texture to concrete.” He personally recommends starting with something such as a Roman slate skin, in part because of its popularity. Another option is a granite skin.
These thin polyurethane skins are easy to work with simply because there’s no wrong way to use them, although Cameron Morgan of Pacific Concrete Images in Laguna Hills, California, observes that when you use them you may still have to score or saw-cut the concrete for proper control joints.
However, once you’re comfortable with those seamless skins, it’s an easy step to move on to mats or stamps with definite patterns.
“Once you get beyond the skins, you can probably handle stamping tools that create a pattern and a texture, with the most popular being the random stone and ashlar slate,” says Morgan. “There are patterns for creating brick and cobblestones in running bond, herringbone, basket-weave and fish-scale-type patterns called European fans.”
Some tool manufacturers offer scores of different designs for stamps, including a variety of stone, brick and wood patterns. Because they leave deeper patterns and even grout lines, stamps are also made of heavier latex than the skins.
“The pattern systems are a heavier-made tool so you can actually walk on them and pound the impressions into the surface of the slab,” says Dave Blasdel, who offers training and technical support to clients of the Aurora, Illinois-based Butterfield Color. “Of course, there are flex stamps for getting into tight areas, but the rigid stamps are twice the thickness of the flex stamps.”
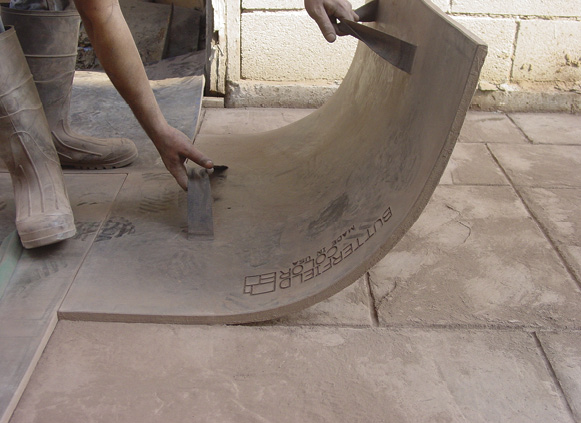
The big problem with patterned stamps is developing the ability to pick them up and reposition them precisely. Steve Maycock, vice president of sales and marketing with Laredo, Texas-based QC Construction Products, is one of several who says the best way to master that part of the job is practice, practice, practice.
Maycock says one option for new imprinters is to set up an area with fine sand, dampen it a bit and then practice lining up the tools and turning them.
One other aspect to be considered when using skins or stamps is whether the job is being done on a freshly poured slab or if it’s going on an overlay. Depending on the tool, it may make a difference.
“With our line, we design them with a quarter-inch overlay in mind,” says Proline’s Irwin. “The only limitation is when you get into groutable patterns. Those get too deep for a quarter-inch overlay.”
Maycock says QC makes an overlay designed specifically to be stampable, and while generally overlays that tend to be more than a half inch can be problematic, “I’d estimate 95 percent of texture mats are relatively shallow in their impressions,” and suitable for overlays, he says.
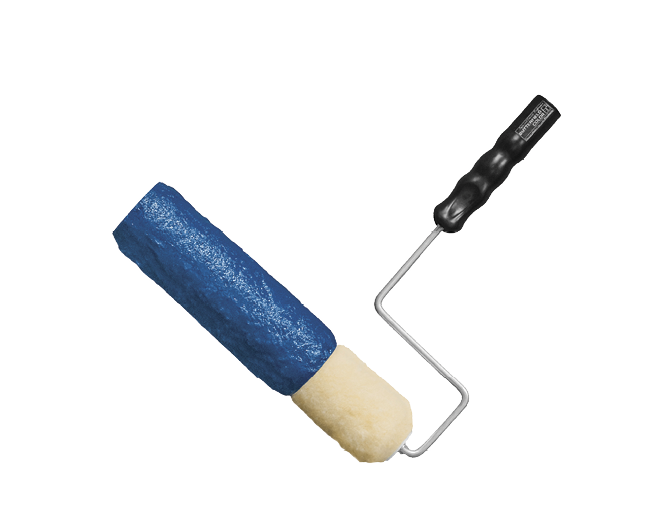
Rolling along
Skins and stamps certainly aren’t the end-all and be-all when it comes to concrete texturing. Rollers are another option, and while they don’t have the learning curve stamps do, they have limitations, especially along walls, in corners and working around objects.
Still, texture rollers can be beneficial when working with overlays, says John Bongiovanni, president of Gibsonia, Pennsylvania-based Bon Tool.
“We offer a seamless texture roller, although there are some that create a joint, as well,” he says. “But, you can imagine trying to roll your texture roller out across a concrete slab 20 feet and then roll it back in the exact same lines. It’s next to impossible.”
The Bon Tool roller has a tapered edge so that as it’s rolled back, no matching is required. By moving it in different directions it can keep the pattern random, Bongiovanni says.
Nathan Giffin, marketing director of Chicago-based Walttools who also owns Vertical Artisans, says he has even taught others to create their own texture rollers from regular paint rollers.
“I brought some of them to Walttools and they began making prototypes,” he says. “They fit on a regular roller sleeve handle. ”
John Reynolds, director of training for Solomon Colors/Brickform in Springfield, Illinois, feels textured rollers are particularly great for doing borders — in certain situations.
“Generally, rollers tend to be for areas that are a little more controlled,” he says. “With stamps there’s a greater degree of flexibility. If there’s a wall or an odd shape or an obstruction, stamps give a little more flexibility for working around them.”
Butterfield’s Blasdel agrees with Bongiovanni that rollers tend to work better on overlays than on slabs, even ones as large as Butterfield’s newest roller design, which is 18 inches wide and has a 3 ½-inch diameter.
“You can save a huge amount of time with an 18-inch roller if you’re doing smaller jobs,” he says. “However, it isn’t heavy enough on a slab to give you enough of an impression. That’s when you need a seamless skin.”
Besides saving time on a job, there’s also less fatigue involved when using a roller. And when it comes to creating borders, many rollers are flexible enough to create curved as well as straight patterns.
Let’s get creative
While skins, stamps and rollers tend to fill the day-to-day needs for many concrete contractors, that’s not to say there aren’t other options out there.
One product that seems to fall in and out of favor — and one could argue is decorative rather than a texture — is stencils. But, for every company such as QC, which has dropped its stencil line, there are others, including Butterfield and Solomon Colors/Brickform, who still find some market for them for both horizontal and vertical concrete.
“Stencils are actually pretty universal,” says Blasdel. “They’re great for doing border systems, but you can also do texture stenciling of entire slabs. They’re popular with tilt-up buildings where they’ll use a stencil system and just roll a little texture over it and make the building look like brick.”
Todd Rose is the sales manager for ready mix and decorative concrete for Brickform’s Mid-South region. He says one attractive thing about stencils is that once you finish the texturing and coloring process and you have pulled the stencil, there’s a totally different-colored grout or imprint line.
And, when used as borders, they can offer a lower-cost option, whether outdoors or in a room that’s done mostly with a seamless texture skin for the main body.
“If a person doesn’t want to spend $20,000-$30,000 on a driveway, they can do something simple with a border stencil on the outside. This really dresses it up for only a couple thousand dollars,” Rose says.
And, he adds, stencils can be much less expensive for beginners to add to their repertoire and more forgiving to work with than stamps. Other texture options include using brooms and brushes, and even trowels. Again, opinions vary as to how decorative broom finishes really are.
Pacific Concrete’s Morgan says a broom finish is standard fare for city sidewalks and driveways. “What you’re doing is breaking the glaze and adding ridges. This makes the concrete isn’t as slippery as it normally would be,” he says.
However, Blasdel says using a broom on colored concrete can be quite decorative. “You can change the color of a concrete slab by brooming it in different directions,” he says. “Say that you have slabs in a 10-by-10 grid. By going in different directions with each one, you can get a look that’s become very popular.”
Proline’s Irwin agrees. He says in many parts of the world concrete is broomed into swirls and other designs.
Still another option involves trowels. Blasdel says they’re just the thing to enhance other texturing methods. “When we educate people, we like to show the versatility of the tools themselves: the rubber urethane mats, the roller systems and the stencil systems,” he says. “Then, we use trowels to install different textures on the surface of the overlay. We can make them look like stone or wood, just by using a trowel.”
As for success with any type of texturing, education is certainly a key. Blasdel says it’s important to familiarize yourself with all aspects of concrete, not just texturing, and Pacific Concrete’s Morgan agrees.
“You have to have a good basic knowledge of concrete and the dynamics behind it,” says Morgan. “You not only have to have good coordination between your placement methods, but also the timing on the trucks, and even the mix plant. Mastering all those aspects is going to make any job go smoother.”
Then, pay close attention to the world around you, especially natural phenomena, says Walttools’ Giffin. Early in his career, he says he would go out and make latex mats of different natural textures he’d find. To this day, he keeps a close eye on Mother Nature’s creations and tries to figure out ways to incorporate her influences into his work.
“Experiment, sample different textures, cross-contaminate with another texture, and see what you get,” he says.
www.brickform.com
www.butterfieldcolor.com
www.bontool.com
www.pacificconcreteimages.com
www.prolinestamps.com
www.qcconprod.com
www.walttools.com