Florida’s Miami Beach is a part of the country known for its high real estate prices, but the penthouse condominium sales price of $60 million for the Faena House Saxony Condo set a new high. The 22-story condo, designed by Pritzker Architecture Prize-winning firm Foster + Partners, comes with all the usual amenities such as an in-house spa and fitness center, a private club, concierge service and a round-the-clock doorman. But what the buyers might not realize is that the complex is reportedly the world’s largest poured-in-place vertical polished concrete project.
The 41-unit building is upheld with 38,000 square feet of poured-in-place structural concrete walls and columns. “Before our patents-pending technology, concrete panels could be poured on the ground, polished with floor grinders and stood up into place or poured in place and polished with hand grinders,” says project manager Patrick Durkin of Vertical Concrete Polishing.
“Polishing with hand grinders is laborious, costly and can produce uneven results. With our vertical polishing method, structural concrete walls can be poured and polished in place,” he says, saving time and producing consistent results.
The machines have it
The walls had already been poured before the developers tried to find someone to polish them. They invited potential polishing contractors, who all used hand grinders for the task, to polish sample areas and bid the job. Most estimated it would take about three years to complete, which the budgeted funds could not cover. Plus, the polished results from hand grinders were not satisfactory.
The developers contacted Mark Richardson, owner of Vertical Concrete Polishing, about the polishing challenge and he developed equipment specifically for the Faena House project.
The machines run up and down along a vertical track and automatically maintain the necessary pressure to polish the wall. The Faena House walls were of various heights and lengths, ranging from 8- to 30-feet tall with some as much as 100-feet long.
“We were learning on the job with this one. That job was perfect in it presented, I would say, 90 percent of the challenges that we will ever face but we won’t have to deal with them again!” Richardson says. “We weren’t happy at the time but hindsight being 20-20, that was the perfect job for us to learn on.”
With this vertical polishing system, the skill is built into the machine and Richardson doesn’t have to rely on artisans skilled with hand grinders.
Improved efficiency
Richardson’s team began work Feb. 10, 2014, and general construction had been going on about two years before that. It took 18 months to complete the polishing job and the first tenant moved in last summer. In the future, Richardson and Durkin estimate, they’ll be able to complete the scope of this type of work in half the time because of the knowledge gained from this job.
“We kept trying our designs and improving them. We built machines to polish curved surfaces and tight spots, such as columns that had only 8 inches of space in between them,” Durkin says.
When it was time to polish the upstairs of the building, Richardson and Durkin were restricted by 9-foot ceilings and standard-size doorways. They designed and built compacted machines that fit into these spaces and moved both horizontally and vertically.
Efficiency increased dramatically as the job progressed, Durkin says. While he remained on the job site, Richardson spent most of his time in his machine shop in Georgia perfecting the machines.
An associate of Richardson, Spencer Maggard, owner of Advance Concrete Services in Atlanta, Georgia, collaborated with Vertical Concrete Polishing to complete the work.
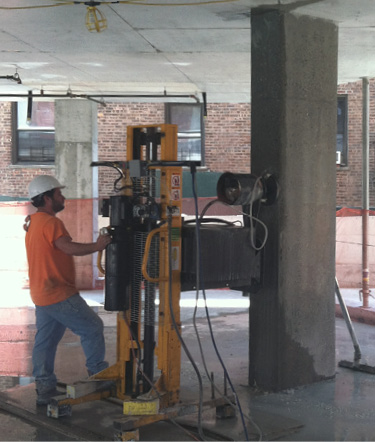
Vertical Concrete Polishing’s innovative system has received positive responses and has attracted international attention, resulting in visits from designers from several other countries. Stateside, the company garnered the 2015 Hanley Wood Innovation Award in the commercial category for its work on the condo.
Richardson’s vertical polishing machines are now being sought after for other projects and applications. He believes that polished walls will become the next market for polished concrete.
Project at a Glance
Project owner and developer: Alan Faena, Faena Group
Concrete Polishing: Vertical Concrete Polishing, Carrolton, Georgia | www.verticalconcretepolishing.com & Advance Concrete Services, Atlanta, Georgia
Architect: Foster + Partners | www.fosterandpartners.com
Scope of project: Machine polish nearly 100 vertical concrete walls ranging in size from 8 to 30 feet. The polishing company developed patented equipment to complete polishing a condominium’s already installed vertical walls.